TECH
Understanding Tool Steel: Types, Properties, and Applications
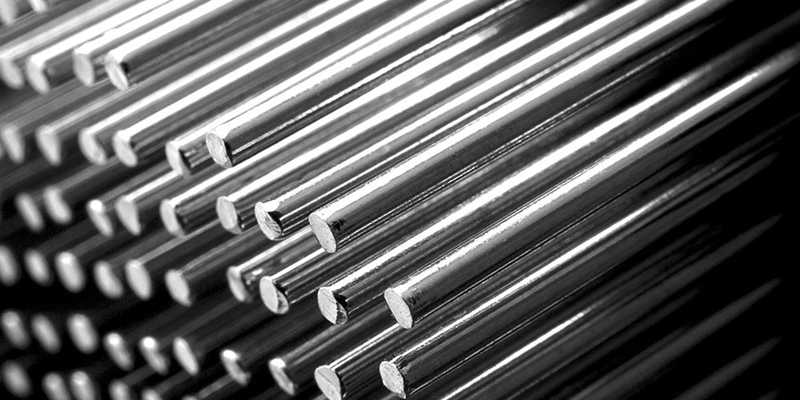
Tool steel is an essential material in industries that rely on strong, resilient, and wear-resistant metal to make tools and machinery. With its specific alloy composition and unique properties, tool steel is the go-to choice for applications requiring durability under high stress and extreme temperatures. This guide offers an in-depth look at tool steel, with a special focus on A2 tool steel, its properties, and applications, as well as the role of tool steel suppliers in the industry.
1. What is Tool Steel?
Tool steel refers to a category of carbon and alloy steels that are specifically formulated for making tools and equipment that cut, shape, or deform other materials. These steels contain specific elements, such as tungsten, molybdenum, vanadium, and chromium, which give them enhanced hardness, wear resistance, and toughness. Tool steel suppliers carefully balance these elements to meet various requirements based on the steel’s intended application.
A2 tool steel, for example, is a high-carbon, high-chromium steel known for its good balance of wear resistance and toughness, making it ideal for precision cutting tools and dies. It belongs to the group of “air-hardening” tool steels, which achieve hardness when cooled in still air, unlike other tool steels that require oil or water quenching.
2. Types of Tool Steel
Tool steel is categorized into various grades based on its characteristics and applications. The most commonly used types include:
Water-Hardening (W-series): This group of tool steels is suitable for low-cost applications requiring high hardness but limited wear resistance. These steels are hardened by water quenching, and while economical, they have lower toughness than other types.
Cold-Work (A, D, and O-series): These tool steels, including A2 tool steel, are designed for applications that operate at relatively low temperatures. They offer high wear resistance and are widely used in applications such as stamping dies, knives, and shear blades.
Hot-Work (H-series): Hot-work tool steels retain their strength and hardness even at elevated temperatures, making them ideal for applications like die casting, forging, and extrusion processes.
High-Speed (M and T-series): These steels are used in high-speed cutting tools, where they can maintain hardness at extremely high temperatures. They are highly alloyed with elements like tungsten and molybdenum.
Shock-Resistant (S-series): This category is designed to withstand impact and shock loading, making it suitable for applications such as chisels, hammers, and punches.
Tool steel suppliers provide each of these grades to industries based on their specific needs, ensuring that each tool or component performs optimally in its intended application.
3. A2 Tool Steel: Composition and Properties
A2 tool steel stands out in the cold-work tool steel category due to its unique composition and properties. It contains approximately 1.0% carbon, 5.0% chromium, and small amounts of molybdenum and vanadium. This composition provides A2 tool steel with a good balance of hardness, toughness, and wear resistance, making it suitable for various applications.
Tool steel suppliers often recommend A2 tool steel for its versatility and stability during heat treatment. The steel undergoes austenitization at 927–982°C (1700–1800°F) and hardens by cooling in air, which reduces the risk of distortion and cracking. Additionally, A2 tool steel offers excellent machinability, allowing manufacturers to achieve precise cuts and shapes.
4. Heat Treatment of A2 Tool Steel
Heat treatment is essential in enhancing the properties of A2 tool steel, especially hardness and wear resistance. Proper heat treatment includes several steps:
1. Preheating: A2 tool steel should be preheated to 677–760°C (1250–1400°F) to prepare it for austenitization.
2. Austenitization: The steel is then heated to 927–982°C (1700–1800°F), where it achieves the desired hardness and strength.
3. Cooling (Air Hardening): Unlike oil-quenched steels, A2 tool steel is air-cooled, reducing the risk of warping or cracking.
4. Tempering: After hardening, the steel is tempered at a lower temperature to improve toughness. Tempering temperatures vary depending on the desired hardness.
Tool steel suppliers and heat-treatment experts ensure that these steps are carefully followed to maximize the performance of A2 tool steel in demanding applications.
5. Applications of A2 Tool Steel
A2 tool steel’s properties make it suitable for a range of applications where wear resistance and toughness are essential. Typical applications include:
Cutting Dies and Punches: A2 tool steel’s hardness and wear resistance make it ideal for cutting dies, punches, and other cold-work applications where tools are exposed to repeated impact.
Shear Blades and Knives: A2 tool steel holds an edge well, making it suitable for shear blades, knives, and other cutting tools that need to maintain sharpness over extended use.
Stamps and Forming Tools: Its toughness and resistance to deformation make A2 tool steel an excellent choice for stamping tools and forming dies.
Gauges and Precision Components: The dimensional stability of A2 tool steel after heat treatment allows for precise manufacturing, which is crucial in gauges and other precision components.
Tool steel suppliers often recommend A2 for these applications due to its ability to withstand wear without significant distortion.
6. Why Tool Steel Suppliers Recommend A2 Tool Steel
Tool steel suppliers frequently recommend A2 tool steel for its excellent performance in cold-work applications, where a balance of hardness and toughness is essential. The alloy’s ability to air-harden is a significant advantage, as it reduces the risk of deformation during heat treatment, ensuring dimensional stability in precision tools. Furthermore, A2’s wear resistance reduces the need for frequent replacement, offering manufacturers cost-effective performance.
Suppliers also highlight A2 tool steel’s machinability, which allows for intricate and precise shapes without compromising the integrity of the material. This combination of benefits makes A2 tool steel a popular choice for both large-scale industrial applications and specialized, high-precision tools.
7. Selecting the Right Tool Steel Suppliers
Choosing reputable tool steel suppliers is crucial in ensuring the quality and consistency of A2 tool steel. High-quality suppliers provide detailed specifications and consistent alloy compositions, ensuring that manufacturers can rely on the steel’s performance across different applications. Furthermore, experienced suppliers offer technical support, helping customers select the best tool steel for their specific needs and advising on appropriate processing techniques.
Tool steel suppliers who specialize in A2 tool steel provide valuable insights into heat treatment, machining, and finishing processes, enabling manufacturers to achieve the best possible results. Working with reliable suppliers ensures that industries can access high-quality materials that meet stringent performance standards.
8. The Future of Tool Steel: Innovations and Trends
The tool steel industry is continually evolving, with advancements in alloy composition and heat-treatment processes driving improvements in performance. Researchers and tool steel suppliers are developing new formulations and processing techniques to further enhance the properties of tool steels, including A2 tool steel. These innovations focus on increasing hardness, toughness, and wear resistance while minimizing the risk of distortion during manufacturing.
In addition, sustainable practices are becoming more prominent, as tool steel suppliers seek to reduce waste and energy consumption. This trend aligns with the increasing demand for eco-friendly materials in manufacturing, ensuring that future tool steels not only meet performance requirements but also contribute to a more sustainable industry.
Conclusion: A2 Tool Steel as an Industry Standard
A2 tool steel is a versatile and reliable material widely used in industries that require precision, wear resistance, and toughness. From cutting dies and punches to shear blades and precision gauges, A2 tool steel’s balanced properties make it ideal for a broad range of applications. Tool steel suppliers play a vital role in ensuring that manufacturers receive consistent, high-quality A2 tool steel tailored to meet specific requirements.
Understanding the unique characteristics of A2 tool steel and working with experienced tool steel suppliers allows manufacturers to make the most of this alloy’s capabilities, ensuring long-lasting, high-performing tools and components. As the tool steel industry continues to innovate, A2 tool steel remains a cornerstone material in manufacturing, trusted for its performance and resilience in demanding applications.
Keep an eye for more news & updates on TechRanker!