TECH
Understanding the Fabrication Challenges of Incoloy 925
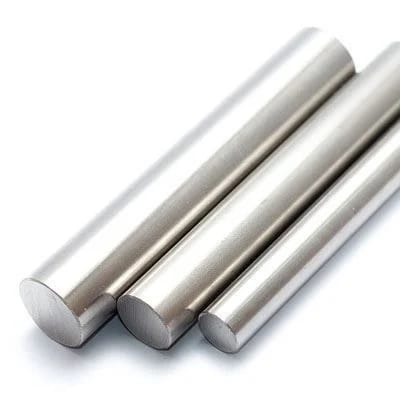
Incoloy 925 is widely used in applications where harsh conditions and high performance are essential. It has become a preferred choice in industries like petrochemical and marine engineering, where materials face corrosive environments and high stress. However, fabricating Incoloy 925 poses a unique set of challenges due to its complex chemical composition and work-hardening characteristics. In this guide, we’ll explore these challenges and discuss techniques that incoloy suppliers and fabricators can use to achieve optimal results.
1. What Makes Incoloy 925 So Challenging to Fabricate?
Incoloy 925 contains a high concentration of nickel, iron, chromium, and other elements that make it incredibly resilient but also difficult to process. Nickel, which forms the alloy’s foundation, gives Incoloy 925 its high strength and resistance to various forms of corrosion. Incoloy suppliers often emphasize this alloy for its durability, but it is precisely this durability that makes it challenging to machine and weld.
The alloy’s work-hardening rate means it becomes harder as it is worked, making processes like machining, cutting, and forming more difficult. Manufacturers must use specialized techniques and equipment to handle the work-hardening properties of Incoloy 925 without causing tool wear or material damage.
2. Machining Incoloy 925: Overcoming Tool Wear and Hardening Issues
Machining is one of the primary challenges when working with Incoloy 925. The alloy’s nickel content, along with other hardening elements, makes it resistant to cutting and prone to causing significant wear on cutting tools. Incoloy suppliers recommend carbide or ceramic tools for machining operations due to their hardness and ability to withstand high temperatures.
To prevent work-hardening, it’s essential to maintain a steady feed rate and avoid letting the cutting tool dwell on the material surface. Using a high feed rate and a sharp, high-quality cutting tool can minimize the amount of heat generated during machining, which in turn reduces the work-hardening effect. Cooling lubricants should also be applied to prevent overheating and to extend the life of cutting tools. These considerations are crucial to achieving precision cuts and minimizing costly tool replacements.
3. The Importance of Heat Treatment for Incoloy 925
Heat treatment plays a significant role in preparing Incoloy 925 for specific applications. Incoloy suppliers often recommend solution annealing and age-hardening treatments to improve the alloy’s mechanical properties. However, conducting these heat treatments can be challenging because precise control over temperature and timing is required to avoid compromising the material’s integrity.
For example, solution annealing involves heating Incoloy 925 to around 1038°C (1900°F) and then rapidly cooling it to prevent grain growth and maintain its fine microstructure. This process optimizes corrosion resistance and mechanical strength but must be done with care to avoid thermal distortion or stress fractures. Understanding the alloy’s response to different heat treatments is key to achieving the desired material characteristics without introducing flaws.
4. Welding Incoloy 925: Mitigating Cracking and Warping
Welding Incoloy 925 can be complex due to its sensitivity to high heat and tendency toward cracking. The alloy’s unique composition requires special welding techniques to avoid introducing weaknesses at the weld joint. Many incoloy suppliers recommend using low-heat input welding methods, such as TIG (Tungsten Inert Gas) welding, to reduce the risk of thermal distortion and cracking.
Preheating the material can help minimize the temperature difference between the weld area and the base material, reducing the likelihood of thermal stress. Post-weld heat treatment may also be necessary to relieve any residual stresses that could lead to cracking or warping. It’s essential to select filler materials compatible with Incoloy 925 to maintain corrosion resistance and mechanical properties at the weld joint.
5. Forming and Bending: Tackling the Alloy’s Rigidity
The strength and rigidity of Incoloy 925 make it resistant to deformation, which can be advantageous in many applications but challenging when it comes to forming or bending. Incoloy suppliers note that cold forming of this alloy requires high-powered equipment and precise techniques to avoid cracks or fractures.
For more demanding bends, warm or hot forming may be necessary, as heating the alloy can make it more pliable and reduce the risk of breakage. However, any heating must be done carefully to avoid unwanted phase changes in the material, which could reduce its corrosion resistance. Manufacturers should be aware that forming at higher temperatures may necessitate additional heat treatments afterward to restore the alloy’s desirable properties.
6. Surface Finishing: Ensuring Corrosion Resistance
A proper surface finish is crucial for Incoloy 925 to maintain its corrosion-resistant properties in aggressive environments. After fabrication, surface treatments such as pickling, passivation, or polishing can help remove impurities and restore the alloy’s protective oxide layer. Incoloy suppliers recommend these treatments to ensure that no surface contamination compromises the alloy’s corrosion resistance.
Passivation, in particular, helps enhance the chromium oxide layer, further protecting the alloy from corrosion. This is especially important in applications where Incoloy 925 will be exposed to chlorides, sulfur compounds, or other harsh substances. Proper surface finishing not only enhances the durability of Incoloy 925 but also improves its aesthetic appeal, which can be a factor in industries like architecture and marine engineering.
7. The Importance of Choosing Reputable Incoloy Suppliers
Given the challenges in fabricating Incoloy 925, it is essential to source the alloy from reputable incoloy suppliers. High-quality suppliers provide materials with consistent composition and reliable documentation, which are critical for achieving the alloy’s full potential in demanding applications. They also offer valuable insights into handling, processing, and fabricating Incoloy 925, which can greatly aid in overcoming the challenges discussed above.
Reputable incoloy suppliers will also provide technical support and may offer tailored advice for specific fabrication processes, helping manufacturers optimize their procedures and reduce the risk of material failure. When working with a complex alloy like Incoloy 925, the quality and support provided by the supplier play a significant role in the success of the final product.
8. Applications That Benefit from Incoloy 925’s Fabrication Challenges
Despite its fabrication challenges, the unique properties of Incoloy 925 make it indispensable for applications requiring extreme durability and corrosion resistance. Industries such as oil and gas, chemical processing, and marine engineering rely on Incoloy 925’s ability to withstand harsh conditions, including exposure to seawater and sulfur-containing gases.
For example, in offshore drilling, Incoloy 925’s strength and resistance to sulfide stress cracking make it ideal for downhole tubing, hangers, and fasteners. These applications benefit from the alloy’s fabrication properties, as they ensure long-term performance without frequent replacements or maintenance. Overcoming the challenges of fabricating Incoloy 925 allows manufacturers to harness these benefits, ensuring reliable performance in critical components.
Conclusion: Overcoming Incoloy 925’s Fabrication Challenges
Incoloy 925 is a remarkable alloy with properties that make it a go-to material in corrosive and high-stress environments. However, fabricating this alloy requires careful consideration of its work-hardening behavior, heat treatment needs, and welding sensitivities. By following best practices and working with experienced incoloy suppliers, manufacturers can overcome these challenges and create components that leverage the full strength and corrosion resistance of Incoloy 925.
From machining and welding to forming and surface finishing, each step in the fabrication process of Incoloy 925 requires expertise and precision. With proper handling and techniques, the alloy’s fabrication challenges become manageable, allowing industries to benefit from its outstanding performance in some of the harshest conditions imaginable.
Keep an eye for more news & updates on TechRanker!